국방품질연구회(DQS)가 전하는 품질 인사이트
DQS 매거진
야전데이터 기반 신뢰성시험 프로파일 설계 방안 연구
2024. 02. 26
글. 국방기술품질원 신뢰성시험분석팀 황수하 선임연구원

서론
최근 국내 개발 무기체계의 기술수준이 고도화, 첨단화됨에 따라 개발단계에서의 신뢰성을 확보하고자 하는 노력이 증가하고 있다. 이러한 추세에 맞게 방위사업규정 및 RAM 업무 지침 등에 개발단계에서 신뢰성을 확보하고자 하는 절차 및 방법 등이 명시되어 있으며, 국방기술품질원 국방신뢰성연구센터에서 이에 관한 기술지원 업무를 수행하고 있다.
과거에는 환경시험을 기본으로 하는 신뢰성시험이 주를 이루었지만, 이는 초기 품질의 결함 등을 확인할 때는 유용하지만 장기간 운용되는 군수품의 수명과 내구성 등을 확인하고 검증하는 것은 한계가 있었다. 현재 규정에는 무기체계 개발시 핵심부품·구성품을 선정하도록 되어 있으며, 선정된 핵심부품·구성품의 신뢰성시험을 통해 RAM 목표값을 검증하도록 되어있다.
여기서 신뢰성시험이란 국방전력발전업무 훈령에 따라 성능시험, 환경시험, 수명시험으로 분류되어 있으며, 통상적으로 수명시험을 의미하는 경우가 많다. RAM 목표값 검증을 위한 수명시험을 설계하기 위해서는 무기체계가 운용되는 임무의 종류 및 환경을 기반으로 노출되는 스트레스의 종류, 조건, 수준 등을 확보하고 이를 근거로 시험프로파일을 설정하여야 한다. 하지만 대부분의 경우 신규 개발되는 무기체계이기 때문에 실제 운용환경을 미리 파악할 수 없고, 대부분의 시험 프로파일은 미군 규격에 제시된 값을 활용하는 경우가 대다수이다.
현재 무기체계의 주요 구성품에 대한 신뢰성시험은 그림 1, 2의 프로파일과 같은 형태로 가속수명시험이 많이 수행되고 있다. 온도, 습도의 경우에는 미군 규격 이외에도 기상청 자료 등을 근거로 조건을 설정하기도 하지만 진동에 경우에는 참고할만한 통계 데이터가 존재하지 않아 그림 1과 같이 MIL-STD-810에 제시된 시험 프로파일이 유일하다. 진동 또한 주요한 수명 저하 요인임에도 불구하고 이러한 이유로 현재 개발단계 신뢰성시험에서는 온도, 습도 등만 고려한 수명시험만 수행되고 있는 실정이다.
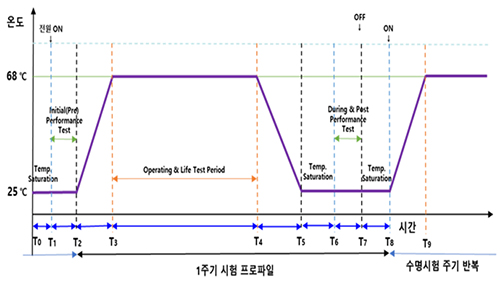
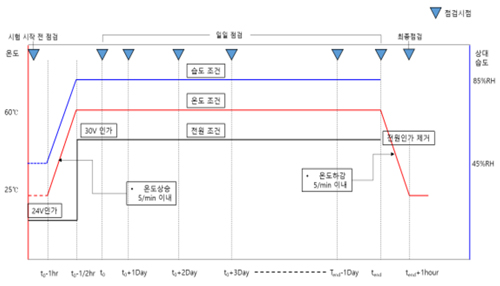
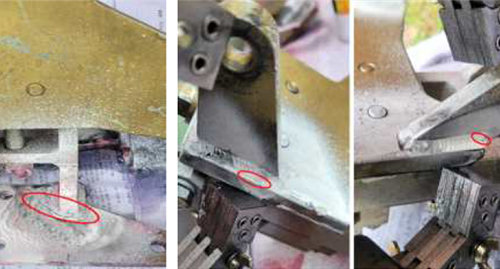
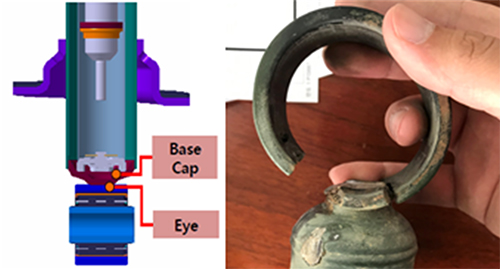
이와 같이 개발과정에서 진동, 충격 등 다양한 환경 요소들에 대하여 수명을 검증하지 못하고 있기 때문에 실제 야전에서 운용중인 무기체계의 경우, 그림 3, 4와 같이 작은 부품류의 균열 및 파손 등이 빈번히 발생하고 있는 실정이다.
최근 강태엽 등은 MIL-STD-810 환경조건 등 이용하여 무기체계의 온도/진동 복합 수명시험 설계 방안에 대한 가이드라인을 제시하기도 하였다. 그들은 개발단계의 무기체계가 노출되는 진동 프로파일을 도출할 수 없기 때문에 그림 5의 예시와 같은 MIL-STD-810G Method 514.6 Category 9의 진동 프로파일의 가혹도를 조정하여 최종적으로 그림 6의 수명입증시험용 복합환경 프로파일을 설계하였다.
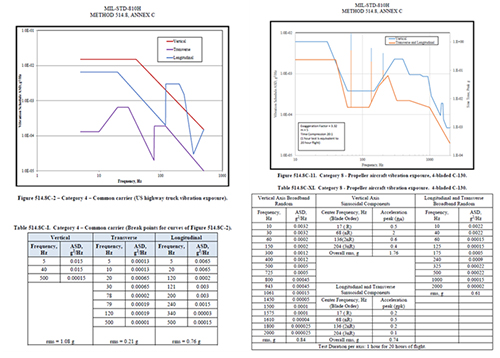
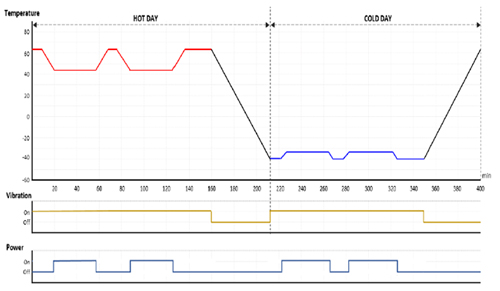
하지만 MIL-STD-810의 진동 프로파일은 미국의 도로상태와 미군 운용기준에 적절하게 표준화된 규격이고 이를 국내 개발된 무기체계에 적용하면 장비에 전달되는 진동수준과 형태가 다르기 때문에 실제 한국군의 운용환경을 모사하는 데에는 한계가 있다.
이렇듯 국방신뢰성연구센터에서는 군수품의 신뢰성을 확보하기 위해 해결해야될 많은 과제들에 직면해있으며 이를 위한 신뢰성에 관한 분석과 다양한 연구들을 수행하고 있다.
본 기고에서는 실제 야전의 환경조건 등을 모사하기 위해 운용되는 무기체계의 주요 환경 데이터를 장기간 동안 무인으로 측정 및 수집하고, 이를 신뢰성시험의 시험조건을 적절하게 설정할 수 있는 데이터 수집장치의 개발과 적용사례, 그리고 향후 발전방향에 관하여 제언하고자 한다.
데이터 수집장치 개발
앞서 언급한 데이터 수집장치는 차량용 블랙박스와 같이, 한번 설치해두면 사람이 직접 계측할 필요 없이 장기간 동안 물리량 데이터를 수집할 수 있는 장치이다.
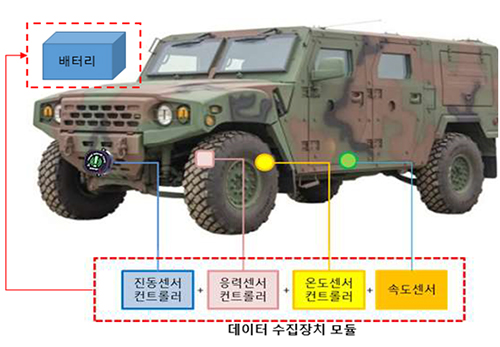
이때 수집하는 데이터의 종류는 기계부품의 신뢰성, 환경시험 조건 등으로 설정할 수 있는 물리량 데이터(진동, 응력, 온도, 회전수 등)로 선정하였으며 이에 대한 개념도는 그림 7과 같다.
위 장비는 효율적인 데이터 수집을 위해 모든 시간에 대한 Raw data를 저장하는 방식이 아닌, 이벤트 트리거 기반으로 데이터를 수집하도록 스마트진동센서와 함께 개발되었다.
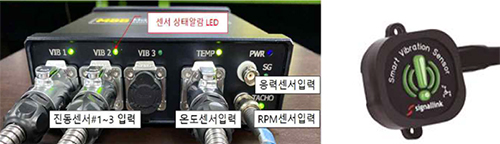
예를들어 스마트진동센서를 통해 기계의 상태를 모니터링하다가 엔진을 가동시키는 등 특정 이벤트가 발생하면, 데이터 수집장치에 전원을 인가하여 Raw data를 저장하고 다른 파라미터의 측정값도 저장하기 시작하는 측정방식이다. 이와 같은 방법은 무기체계에 부착하여 장기간동안 진행되는 훈련 및 작전기간중 노출되는 야전환경 데이터를 수집하는데 효율적인 방법이다.
야전데이터 수집 및 적용
본 연구에서는 개발된 데이터 수집장치를 실제 적용하기 위해 K21 보병전투차량의 다빈도 고장품목 중 “체계제어용 컴퓨터”를 선정하여 훈련중 노출되는 야전데이터를 획득하였다. 데이터 획득을 위한 시험 셋업은 그림 9와 같으며 대상 시험장비 상/하부에 진동센서를 부착하고, 내부 온도 측정을 위한 Thermocouple을 설치하였다. 데이터는 해당 부대 기동훈련중 약 5일간의 기간동안 획득하였으며, 전체적인 진동 및 온도의 경향은 그림 10 ~ 12에 나타내었다.
이때 센서 설정을 통해 Trigger Level 이상에서는 진동 주파수 스펙트럼 데이터를 동시에 저장하도록 데이터 수집장치를 설정하였고, 그 결과 그림 13과 같이 약 42000개의 FFT 데이터를 획득하였다.
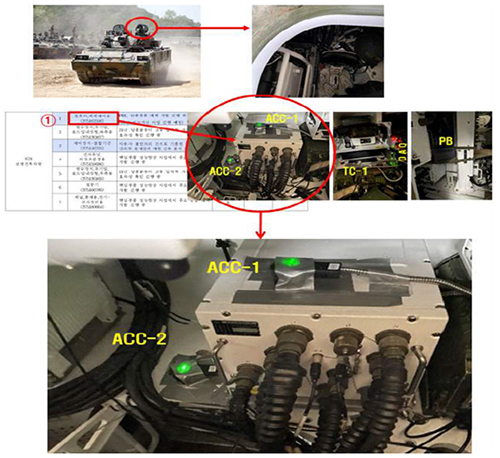
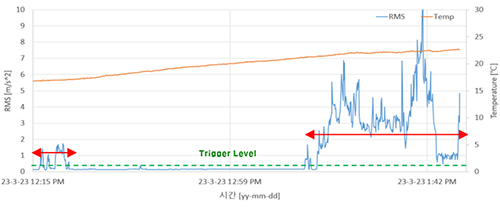
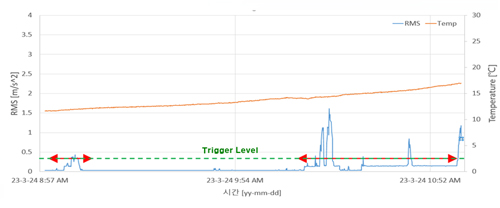
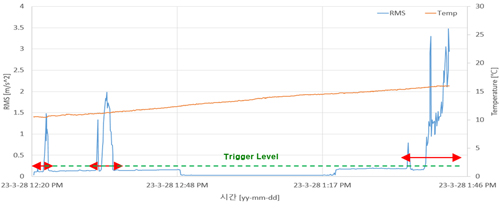
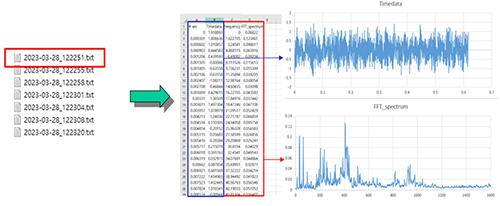
획득한 42000개의 FFT 데이터의 대푯값을 보수적인 관점으로 주파수당 최대값(Envelop Limit)으로 설정하였고, 그림 14와 같이 하나의 그래프로 나타내었다.
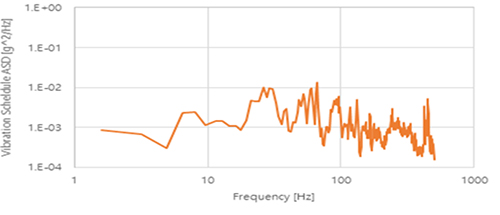
한편 체계제어용 컴퓨터의 신뢰성을 확인하기 위해서는 국방규격상 제시된 보증시간인 3058시간 동안 시험을 수행하여야 하는데, 이는 현실적으로 불가능한 시간이다. 이러한 사유로 MIL-STD-810에서는 Miner's Rule에 따라 가속시험 관계식을 제시하고 있으며 약 2주간의 신뢰성시험(진동내구시험)을 한다고 가정하였을 때, 그림 14의 프로파일에 가속계수 1.85을 적용하면 3058시간과 동일한 효과를 볼 수 있다.
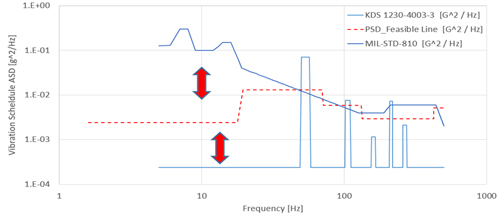
그림 15는 최종적으로 도출된 야전데이터를 기반으로한 진동시험 프로파일과 체계제어용 컴퓨터 국방규격상 제시된 진동시험 프로파일, 그리고 MIL-STD-810에 제시된 수송진동 프로파일을 비교한 그래프이다.
그림의 MIL-STD-810 프로파일의 경우, 비포장도로의 노면상태를 기준으로 표준화되었기 때문에 저주파 진동이 매우 크지만, 야전데이터 기반 프로파일의 경우, 운용부대의 훈련로가 대부분 포장도로로 이루어졌기 때문에 저주파 영역에서의 진동값이 차이가 있음을 확인하였다. 한편, 국방규격상의 제시된 프로파일은 야전데이터 기반의 프로파일 값보다 50 Hz 이하의 저주파에서 매우 낮아서 실제 무기체계의 탑재장비가 받는 스트레스 조건을 반영하지 못하는 것으로 보이며, 추후 규격 등을실제 진동데이터 기반의 프로파일로 수정하여야만 야전 무기체계의 신뢰성을 검증할 수 있을 것이다.
결론
본 연구에서는 야전데이터를 무인으로 장기간 측정할 수 있는 데이터 수집장치를 개발하였고, 개발된 데이터 수집장치를 활용하여 실제 야전에서 운용중인 무기체계의 탑재장비에 설치하여 노출되는 스트레스 데이터를 수집하였다. 또한 측정된 데이터를 기반으로 현재 국방규격에 제시되어 있는 진동시험 프로파일의 문제점과 개선방안 등을 제시하고자 하였다.
데이터 수집장치는 MBB라고 명명하였으며 스마트진동센서와 함께 개발하여 센서를 설치한 이후에 사람의 개입 없이 무인으로 데이터가 수집되는 차량용 블랙박스와 같은 형태로 측정되는 방법으로 고안하였다. 이는 모든 데이터를 모든 시간에 대하여 저장하는 것이 아니라 스마트진동센서를 통해 진동을 모니터링하다가, 특정 설정 조건 이상의 스트레스가 발생한 이후부터 진동, 응력 등의 시간데이터(Raw data)를 저장하는 방식이 가능하도록 개발하였고, 상용 가속도계와의 비교/검증시험을 통해 오차가 매우 미미한 수준임을 확인하였다.
이후 다빈도 고장품목 중 하나인 K21 보병전투차량의 체계제어용 컴퓨터를 시험 대상으로 선정하고, 기계화보병대대의 협조를 통해 훈련 중 시험대상품이 노출되는 야전데이터를 수집하였다. 약 5일간의 기동훈련 간 야전데이터를 수집하였고, 이를 통해 신뢰성시험에 활용할 수 있는 진동시험 프로파일을 설계하였다. 설계된 진동시험 프로파일은 MIL-STD-810과 체계제어용 컴퓨터의 국방규격에 제시된 프로파일과 비교하였는데, 국방규격에 제시된 프로파일의 경우, 실제 탑재 부품이 받는 스트레스 조건을 반영하지 못하여 저주파 영역의 진동 레벨이 매우 낮은 것을 확인하였다.
본 연구를 통해 개발된 데이터 수집장치는 추후 앞서 기술된 신뢰성시험 설계 이외에도 고장원인 분석 등 다방면으로 활용가치가 있을 것으로 기대되며, 야전에서 획득한 데이터를 개발단계에 환류함으로서 군수품의 신뢰성을 제고할 수 있을것으로 전망한다.
- 참고문헌
-
- 1. Tae Yeob Kang, Donghwan Seo, Joonki Min, Kangyoug Lee, Sungkyu Kim, Jeongpyo Hong, Ilyoung Yang, Sangwoo Yu,“Design Guideline for Non-Accelerated Life Testing on Components of Defense Systems by Modifying MIL-STD-810 Testing Profiles,” J. of Appl. Rel., vol. 21, no. 1, pp. 69-78, 2021.
- 2. Yun Seongho, Yoo Youngsu, Kim Seonggon, Kim Seonjin, "The user complaints analysis report of Korean light tactical vehicle", Research and Investigation Report, Defense Agency for Technology and Quality, Korea, pp. 1-110 2019.
- 3. 김대환, 박인기, 김준엽, “랜덤 진동 규격 개발 I: 차량 실측 진동 데이터를 이용한 수송진동 규격 생성”, 한공항공우주학회 학술발표회 초록집, pp. 972-975, 2015
- 4. Jae-Sang Cho, Chang-Nam Kim, Do-Hyuk Kwak, Seoung-Han Lee, Eui-Bong Jeong and Gu-Hyun Ryu,“Derivation of Vibration Test Profile for Equipment Mounted in Tracked Vehicle”, Trans. Korean. Soc. Noise Vib. Eng., vol. 30, no. 3, pp. 249-254, 2020.