국방에 기여하는 국방기술품질원의 이야기
기술로 품질로
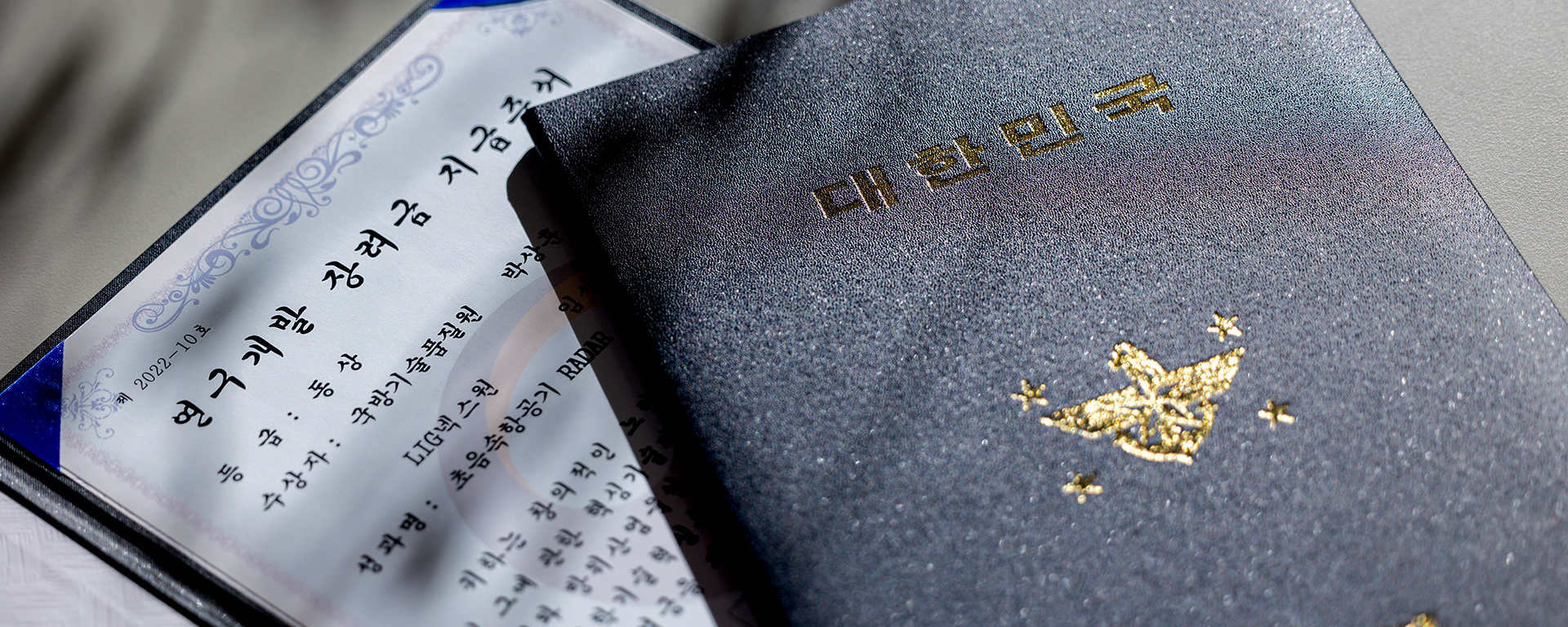
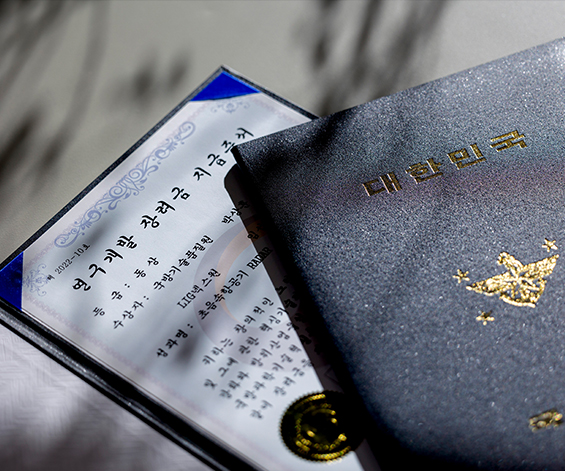
2mm의 차이, 2L의 땀방울
2022 연구개발 장려금 우수과제 시리즈 - 동상
글 권혜란
사진 차유진
2022 연구개발 장려금 우수과제
- 연구개발 장려금이란?
- 방위사업청은 국방 분야의 연구개발 활성화를 촉진하고 국방 분야 연구원과 방위산업 종사자들을 격려하는 활동의 일환으로 연구개발 장려금 제도를 운영하고 있다. 2022년 장려금은 금상 5천만 원, 은상 3천만 원, 동상 2천만 원, 장려상 1천만 원으로 32건의 과제에 총 5억 9천만 원이 지급됐다. 국방기술품질원도 동상 1건, 장려상 2건을 수상했다.

초음속 항공기 레이다 전기적·기계적 강건성 확보를 통한 항공기 운용성 향상
- 대표 연구자: 항공2팀 박상훈 선임연구원
문제점
‘초음속 항공기인 FA-50의 화력통제 레이다 다빈도 불량 발생’
아무리 크기가 작더라도 부품의 불량은 전체 운용에 영향을 주기 때문에 무기체계의 신뢰성과 직결된다. 불량 발생 빈도까지 높다면 상황은 더 어려워질 수밖에 없다. FA-50의 경우가 그랬다. FA-50에 탑재되는 화력통제 레이다의 불량은 전체 운용 항공기의 26.3%에서 발생했다. 이로 인해 항공기 가동률 저하는 물론이고 불량으로 인한 정비비용도 약 28억 원(추산)이 소요된다. 게다가 원 제작사의 AS 기간 만료로 추가적 기술지원이 힘든 상황까지 겹쳤다.
문제 발생 원인
불량이 발생한 화력통제 레이다(FCR: Fire Control Radar)는 항공기의 필수 구성품이다. 전자기파를 방사하여 반사된 신호를 수신하여 표적을 탐지 및 식별, 추적한다. 사람으로 치면 눈과 같은 역할을 한다. 화력통제 레이다의 전기적 신호처리는 아래 그림과 같이 제어·신호처리를 담당하는 집적회로(IC: Integrated Circuit)와 신호처리의 결과를 전달하는 인쇄회로기판(PCB: Printed Circuit Board)으로 구성된다.
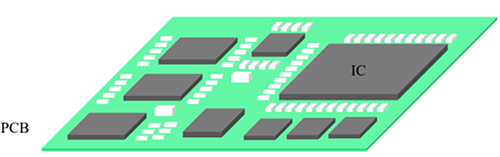
현재는 기술의 발전에 따라 IC가 점차 소형화되는 추세다. IC가 몸집을 줄이는 만큼 항공기 공간, 중량 설계 등에서 이점이 생긴다. 하지만 내구성 측면에서는 이야기가 달라진다. IC와 PCB를 전기적으로 접촉하고 연결하는 납땜(Solder Ball)도 함께 소형화되기 때문이다. 이는 IC와 PCB의 물리적 결합 약화를 야기한다. 특히 임무 수행을 위해 이착륙을 반복하고 고온과 저온의 상황을 반복하며 비행하는 FA-50 항공기의 특성상 IC의 소형화로 인한 납땜 문제에 더욱 취약했다. 이러한 요인이 겹쳐 FA-50 화력통제 레이다(FCR) 전류구동증폭기(DAU: Drive Amplifier Unit)의 제어 및 임무 수행 문제가 다빈도로 발생했다.
해결 과정
원인분석을 위해 CT, X-RAY와 같은 비파괴 검사를 통해 고장 현상의 근본 원인 및 개선안에 대해 분석하고자 하였으나 균열과 같은 특이점을 확인할 수 없었다. 문제를 해결하기 위해서 체계적인 원인분석 및 개선안을 도출하는 계획을 4단계로 수립하고 수행했다.
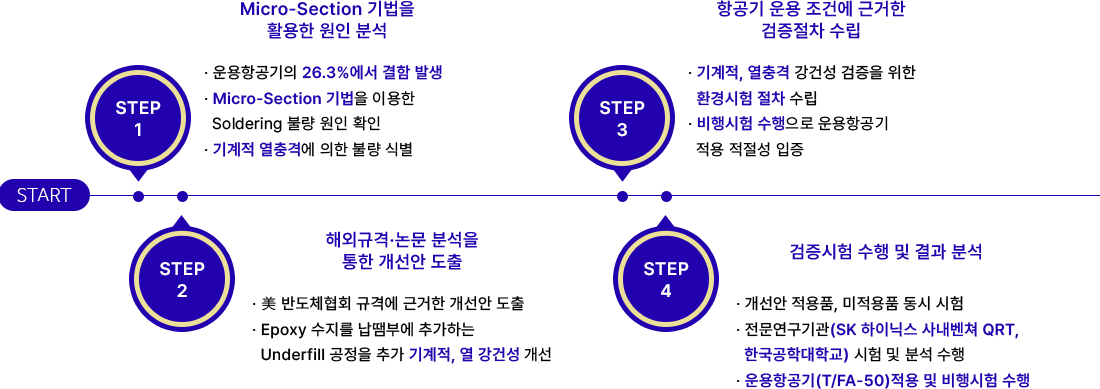
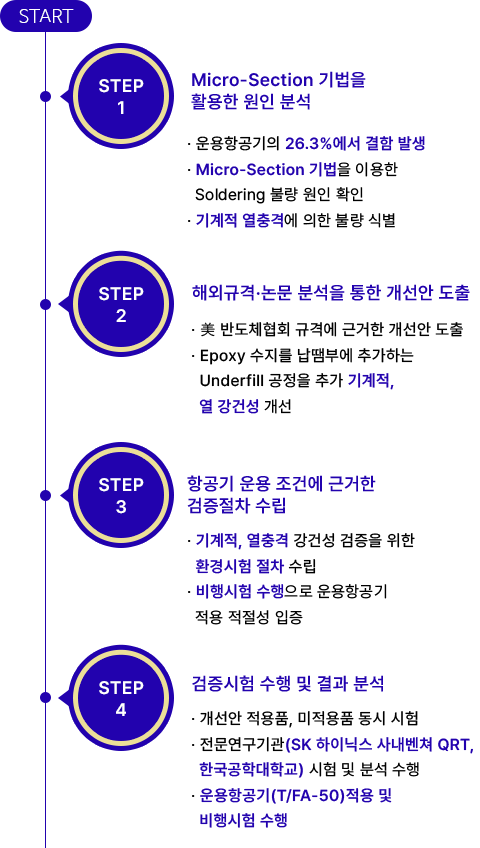
-
- STEP 1. 단층분석(Micro-Section) 기법을 통한 원인 분석
- CT, X-RAY로 발견되지 않았던 납땜 균열의 불량현상의 확인을 위해 단층분석 기법을 활용했다. 단층분석 기법은 인쇄회로기판, 납땜을 물리적으로 절단하여 균열을 확인하는 파괴시험으로 CT, X-RAY로 발견되지 않는 미세 균열을 확인할 수 있다.
-
- STEP 2. 해외규격·논문 분석을 통한 개선안 도출 연구
- 균열을 개선하기 위해 해외규격, 관련 논문을 분석한 결과, 열·기계적 피로에 의한 납땜 균열을 방지하기 위해 언더필(Underfill) 공정이 필요할 것으로 판단했다. 언더필은 절연 수지를 이용하여 납땜부 하단을 메우는 공법으로 물리적 충격(낙하, PCB 변위 충격 등), 화학적 충격(사용 온도 변화의 열 충격 등) 등의 내성 확보를 통해 열·기계적 피로를 감소시킨다.
-
- STEP 3-4. 항공기 운용 조건에 근거한 검증절차 수립 및 검증시험 수행·결과 분석
- 개선안인 언더필 공법 적용 후 기계적, 열 충격에 의한 강건성 검증이 필요했다. 강건성 확인을 위해 환경시험 및 비행시험 계획을 수립했으며 검증시험 후 결과를 분석했다. 그 결과, 개선안을 적용하지 않은 IC에서는 납땜의 미세한 균열을 확인하였으나, 개선안인 언더필을 적용한 제품은 정상으로 확인되었다.
성과
이번 FA-50의 화력통제 레이다 불량 개선 사례에는 다양한 성과가 연결된다. 소요군의 애로사항을 신속하게 해결하여 항공기 가동률 향상에 기여했으며, 언더필 공법 적용 등을 통해 실질적인 예산 절감 효과도 누렸다. 구체적인 예로, 개선안 적용 등으로 정비 시간(MTTR)을 11.5시간 단축했으며 동시에 28.08억의 정비비용 절감 효과를 얻었다. 또한 기존 대비 신뢰도(MTBF) 역시 21.6배 향상된 것으로 나타났다. 이번 개선안은 현재 개발·양산되고 있는 KF-21, TA-50 Block 2 사업의 항공전자장비에 적용되어 소요군의 운용성 확보에 기여할 예정이다. 이와 같은 성과를 통해 FA-50 화력통제 레이다 불량 개선 사례는 ‘FA-50 품질개선을 통한 장비 운용비용 절감 및 RAM 향상 유공’으로 국방부 장관 감사장을 받으며, 대내외적으로 우수성을 인정받았다.

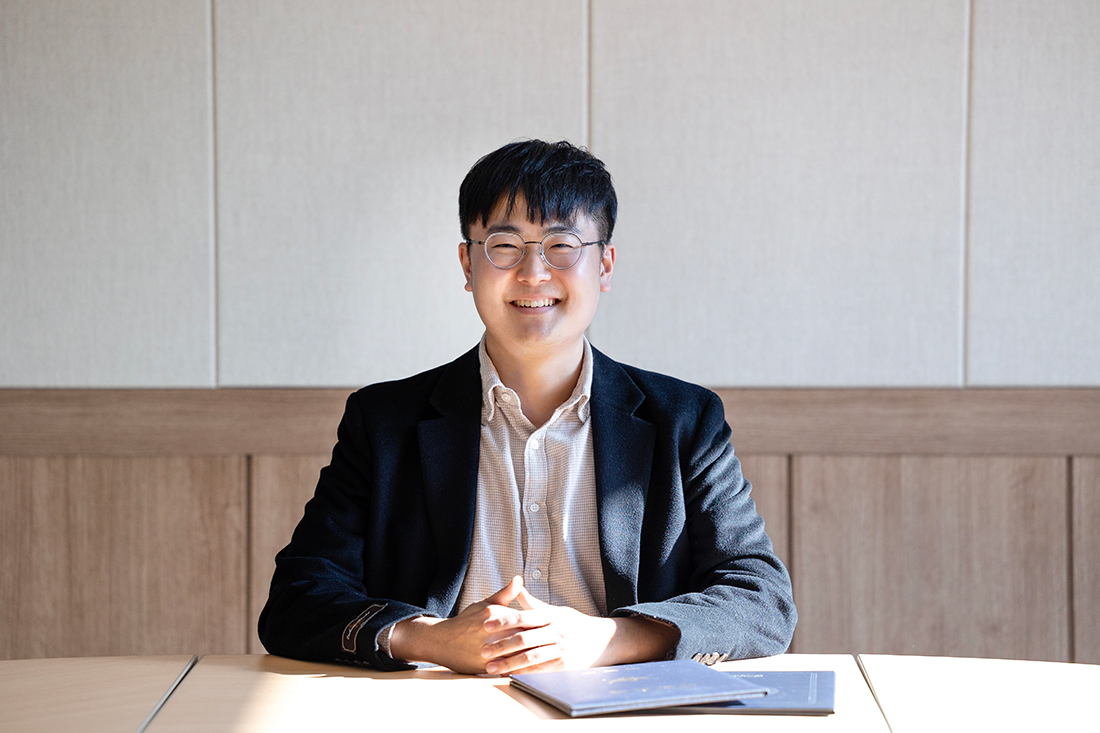
FA-50 화력통제 레이다 불량 소식을 처음 접했을 때 어떠셨나요?
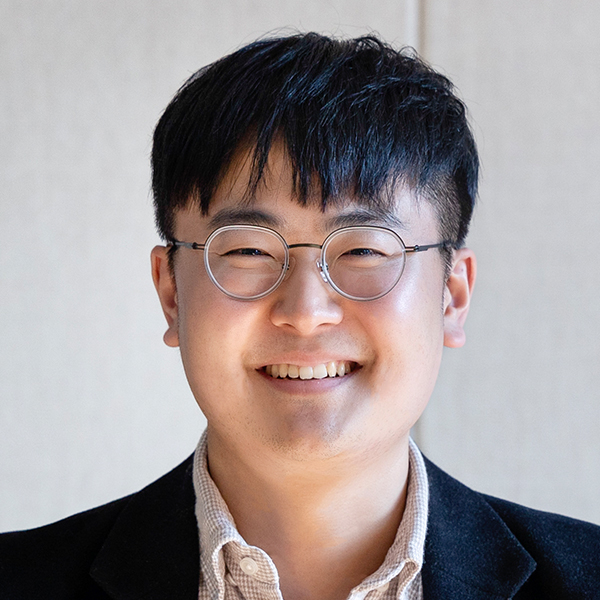
항공2팀 박상훈 선임연구원 FA-50 전체 운용 항공기의 26.3%에서 결함이 발생한 상황이라 원인 분석 및 개선안 도출이 시급했죠. 게다가 FA-50뿐만 아니라 TA-50 Block-2 양산까지 코앞으로 다가온 시기라 아찔했습니다. 그래서 어떻게든 최대한 신속하고 정확하게 해결해야겠다는 마음이 가장 컸습니다.
문제해결을 위한 본인만의 아이디어 도출 방법이 있다면 소개 부탁드립니다.
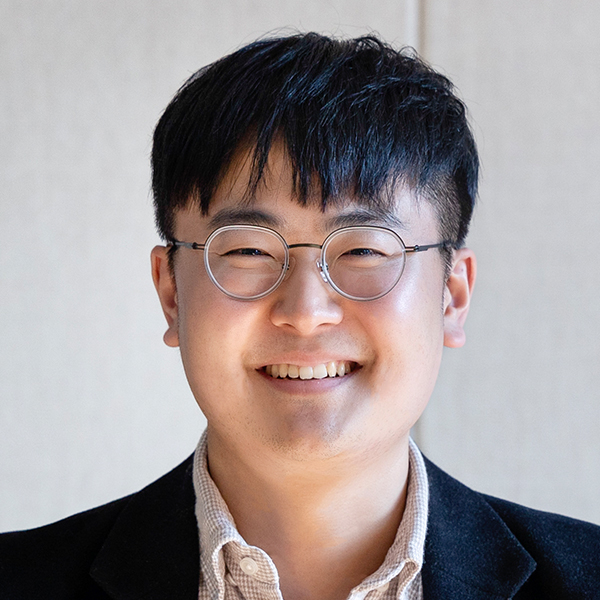
항공2팀 박상훈 선임연구원 문제를 해결하는 과정에선 논리적 사고와 창의력이 중요하잖아요. 브레인스토밍이 도움이 많이 되는 것 같아요. 그리고 타인의 경험을 초석으로 삼으려고 해요. 비슷한 사례를 이미 해결해 보신 다른 분들께 기법이나 노하우를 많이 얻으려고 노력했어요. 입사 전 민수 분야에서 일한 경험이 있어서 IPC(국제전자산업표준협회), JEDEC(국제반도체표준협의기구)와 같은 규격 및 고장 발생 메커니즘에 대한 표준서 등을 많이 참고하는 편입니다.
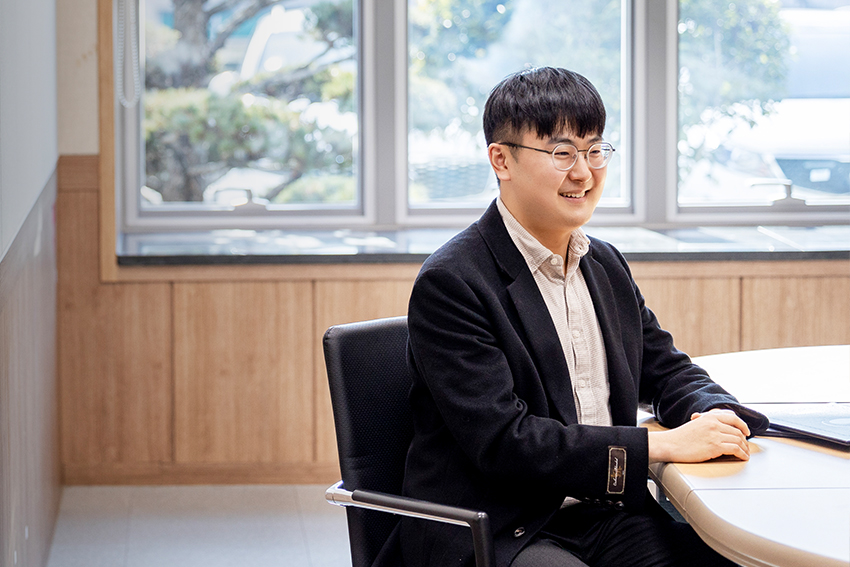
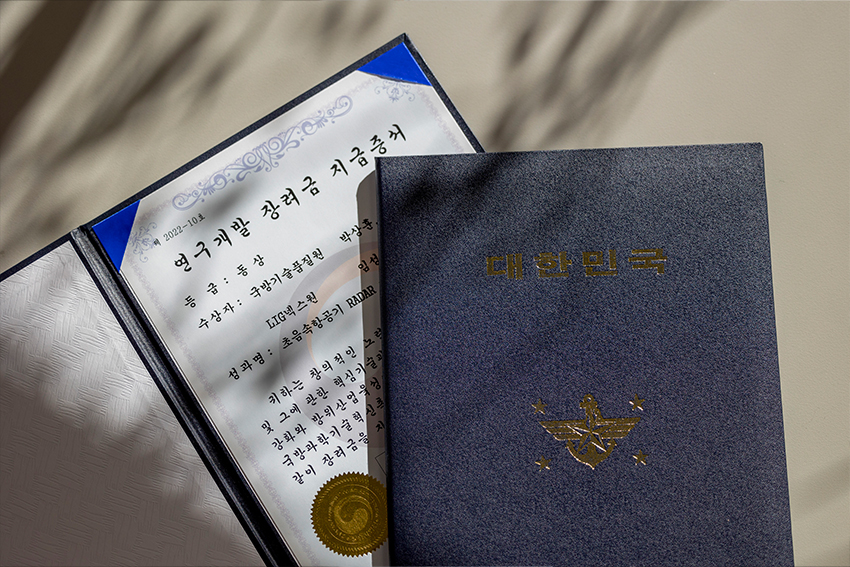
무기체계의 ‘신뢰성’은 거듭 강조해도 부족함이 없죠. 연구원님께 신뢰성은 어떤 의미인가요?
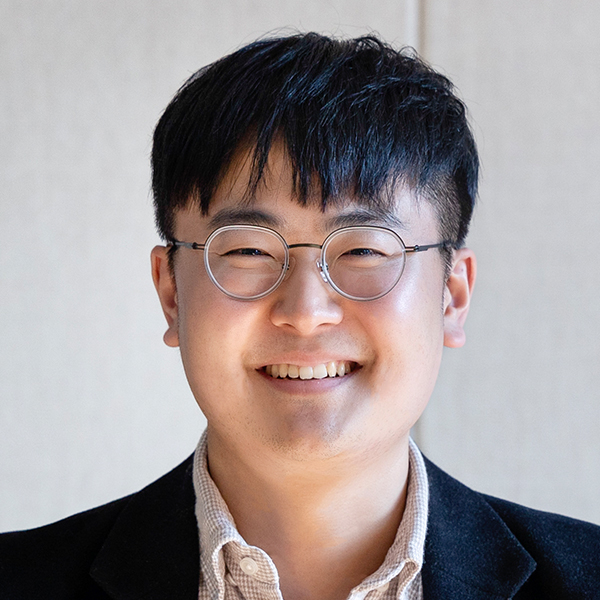
항공2팀 박상훈 선임연구원 신뢰성은 저에게 ‘가족’입니다. 가족처럼 항상 소중하게 지켜야 할 존재이자 가치이기 때문이죠. 무기체계가 양산단계에 들어가면 개발단계에서 예상하지 못한 이슈가 간헐적으로 발생할 때가 있습니다. 이러한 문제는 운용성이나 작전수행능력 감소로 이어지기 때문에 신뢰성은 저에게 반드시 지키고 사수해야 하는 중요한 요소입니다.
앞으로의 연구 활동 및 포부가 궁금합니다.
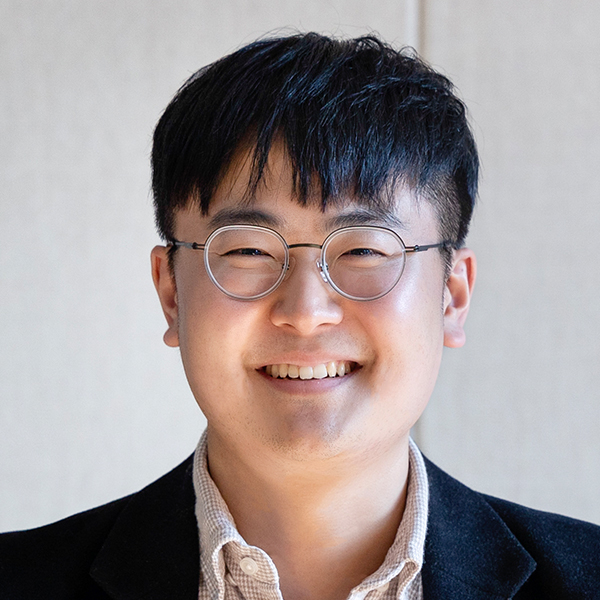
항공2팀 박상훈 선임연구원 중요하지 않은 부품이 없지만 2mm의 작은 납땜(Solder Ball) 때문에 커다란 항공기가 멈출 수 있다는 걸 보면서 사소한 작은 부분도 크게 생각해야 된다는 것을 깨달았습니다. 이번 불량을 해결하면서 2L의 땀은 흘린 것 같아요(웃음). 앞으로는 고객에게 인도되기 전에 이러한 불량 문제를 개선할 수 있도록 프로세스, 공법을 개발하는 연구를 수행하고 싶습니다.
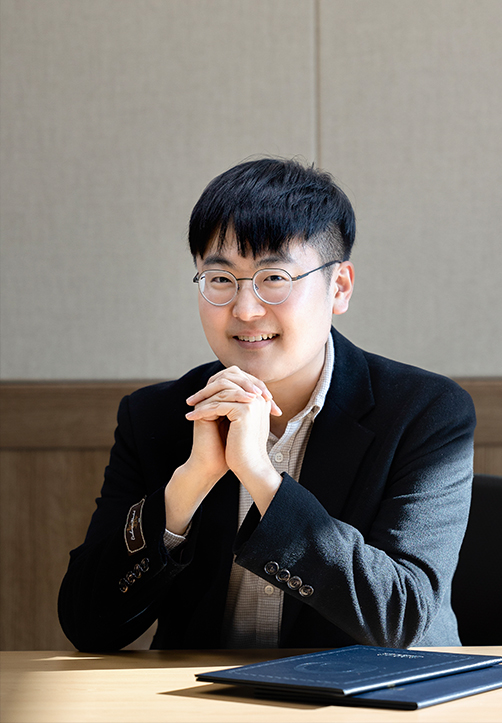
끝으로 연구개발 장려금 수상에 대한 소감 부탁드립니다.
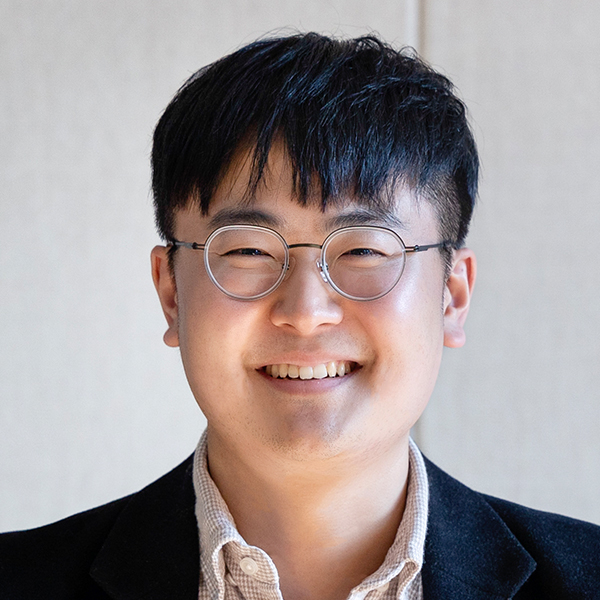
항공2팀 박상훈 선임연구원 예상치 못한 불량을 해결하는데 가장 중요한 부분은 이미 발생한 문제를 얼마나 신속하고 정확하게 해결하느냐가 중요하죠. 국방기술품질원이 개선안을 제안하고 최종적으로 기술변경이 이뤄지기까지 약 9개월이란 시간이 소요되었어요. 고민하고 고뇌했던 도전의 시간들이 2022년 연구개발 장려금 ‘동상’으로까지 이어져 기쁩니다.