국방품질연구회(DQS)가 전하는 품질 인사이트
DQS 매거진
통신,항법장치 생산/검사공정 혁신을 통한 비용 절감
2023. 11. 09
글. 단암시스템즈(주) 최도원 품질보증부서장

배경
최근 외부 환경은 K-방산 수출 활성화에 따른 고객사 원가 경쟁력 요구, 높은 수준의 품질을 요구하며 내부 환경은 생산/검사 공정 비효율 발생에 따른 생산 시스템 고도화가 필요하여 통신,항법장치 생산/검사 공정 혁신을 통한 비용 절감 활동을 하게 되었습니다.
혁신과제선정 및 현상파악
통신,항법장치 생산공정, 시험공정, 검사공정 중 총 8개의 핵심과제가 선정되었다.
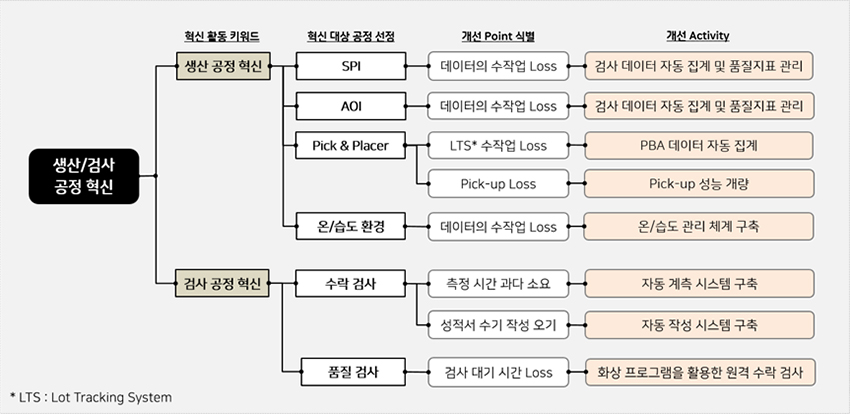
8개 핵심과제는 큰 범주에서 생산공정과 검사공정으로 분류되었으며, 각 세부 활동 항목의 현 수준 파악 후 활동목표를 수립하였다.
활동 항목 | 현재 수준 | 활동 목표 |
---|---|---|
검사 데이터 자동 집계 및 품질지표 관리 (SPI/Pick&Place/AOI) |
118 시간/년 | 자동집계 |
PBA 데이터 자동 집계 및 Pick-up 성능 개량 |
3,832 ppm (198시간/년) |
1,000 ppm (자동집계) |
온/습도 관리 체계 구축 | 12 시간/년 | 자동 모니터링 |
시험 자동화 시스템 구축 | 1,489 시간/년 | 229 시간/년 |
원격 화상 수락 검사 | 120 시간/년 | 비대면 검사 |
표 1. 세부활동 항목 및 활동목표
혁신 대상 세부수행 활동 (5개 부문)
SPI/AOI 검사데이터 자동집계 및 품질지표 관리
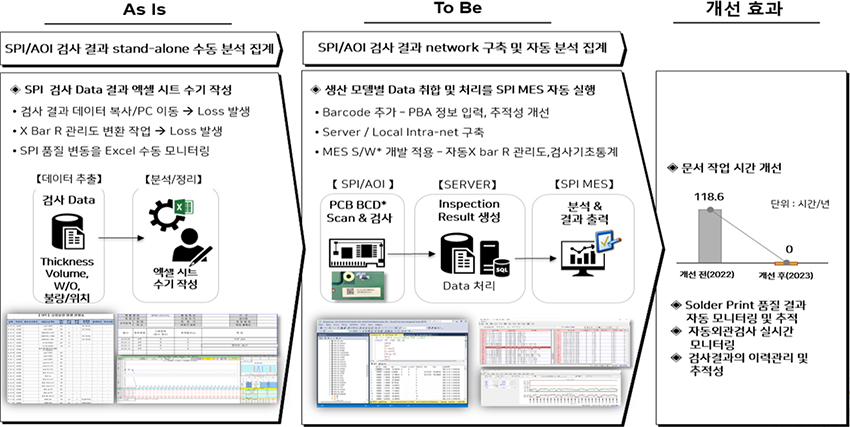
PBA 데이터 자동집계 및 Pick-up 성능개량
PBA(Printed Board Assembly) Pick&Place 공정의, ‘부품 오장착 불량 위험성’, ‘부품이력 수기기록(추적성)’, ‘부품 낙하로 생산성 저하‘ 등의 문제점을 해결하기 위해
- 공압 Feeder를 전동 Auto Smart Feeder 로 변경
- 데이터 자동 집계를 위한 Full-IT system 구축
- 부품의 모든 정보(품번, Lot-No, S/N)를 자동으로 추적/식별가능한 MES 시스템 구축
등의 활동을 통하여 SMT 생산공정의 Risk 및 Loss를 해결할 수 있었다.

온습도 관리 체계 구축
온습도 관리규격이탈로 현장 보관/작업 중인 부품 및 PBA에 심각한 품질 저하의 요인이 될 수 있다. 이를 위해 항온항습장치를 설치 운영하나, 목시에 의존한 온습도 관리규격모니터링 및 수기로 이력관리/주기체크하는 실정이었다. 이를 개선하고자 자동 온습도 모니터링&알람장치를 구축하여 관리규격 이탈 시 자동으로 경고음 발생 및 데이터 서버기록으로 실시간 현장 온습도 모니터링 관리 체계를 구축 하였다.
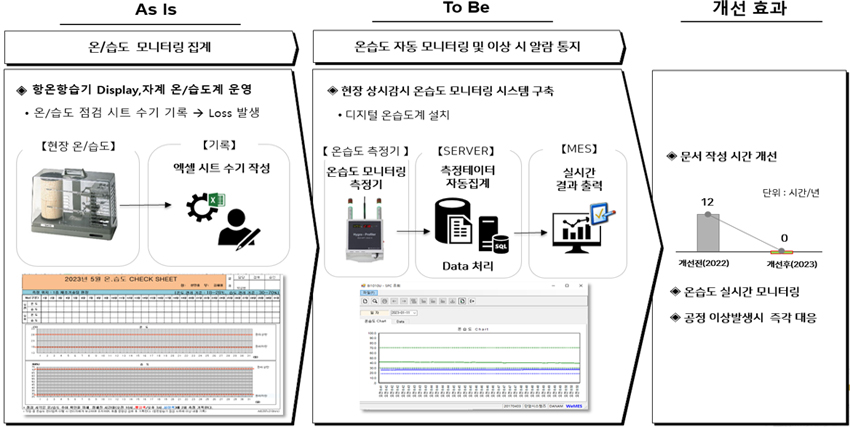
자동계측/작성 시스템 구축
기존 제품 성능테스트를 매뉴얼 테스트하여 발생되는 세가지 애로사항이 식별되었다. 「오기발생으로 고객 불만족 증가」, 「작업자 스킬에 의존」, 「시험 장시간 소요 및 성적서 수기작성으로 공수 Loss 등」. 이를 해결목적으로 당사 보유 계측기 자동제어 측정기술을 기반으로 ATS(Auto Test System)을 자체적으로 구축하여 상기 애로사항을 모두 개선할 수 있었다. 이 기술은 현재 당사 텔레메트리, 데이터링크, 비콘 및 항법분야 RF 제품군으로 확대 적용 중에 있다.
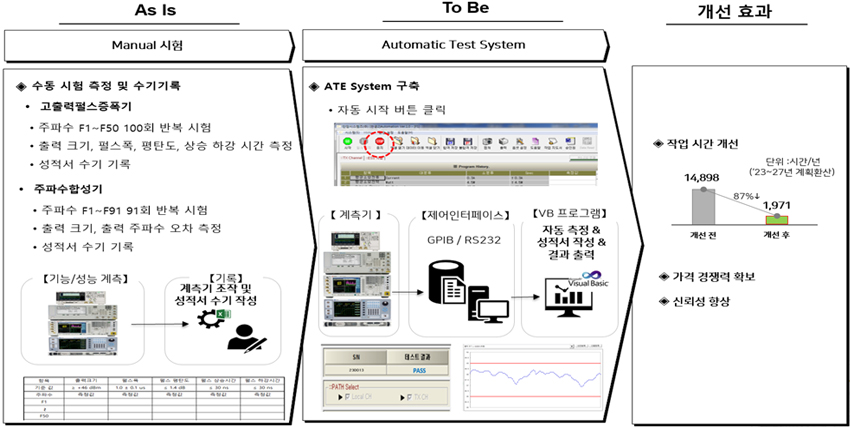
화상프로그램을 활용한 원격 검사
본 개선활동은 아래 두가지 Loss를 해결할 목적으로 추진하였다.
첫째, 일솜씨 부적합이 많은 원거리 위치 협력업체의 개선 필요성
둘째, 고객수락검사 대기/일정변경 Loss
추진한 개선활동으로, Remote 비대면 검사시스템을 구축하여 협력업체에서 당사로 제품 납품 전 누적발생 부적합 목록이 반영된 일솜씨 실패사례 Check-List를 활용, 최종 납품 Point에서 양사 간 중점확인 수행하여 불량유출을 예방할 수 있었고, 이를 수행한 경험을 바탕으로 고객 비대면 수락검사 정책에 따라 수락검사 Loss를 최소화 할 수 있었다.
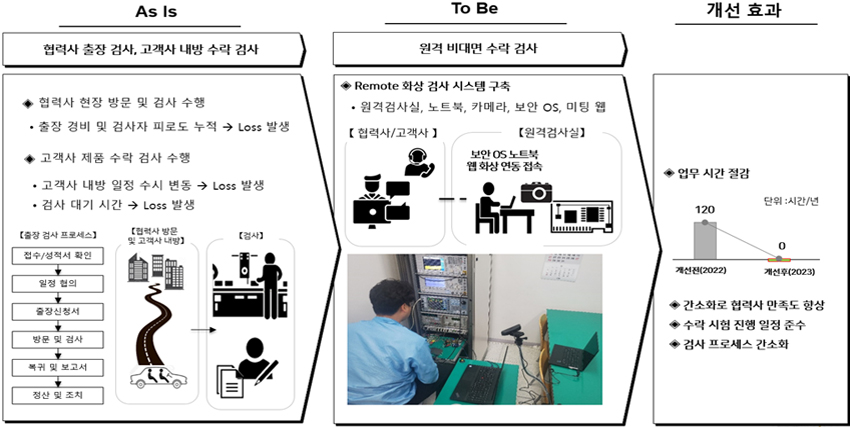
결론
금번 통신, 항법장치 생산/검사공정 혁신활동을 토대로 공정 간 숨겨져 있던 Loss개선으로 아래와같은 개선 성과를 달성할 수 있었다.
- 기존 데이터 수동집계(SPI/AOI/P&P/온습도)작업을 실시간 자동집계 시스템구축을 통하여 년간 약 328 시간을 절약하였으며,
- 시험 공정 자동화 및 원격화상검사 시스템 구축을 통하여 약 87%의 시간절감 효과를 얻을 수 있었다. (‘23~’27년 납품 수량 적용 시 : 15,018시간 → 1,971시간 절감)
금액으로 환산할 경우, 장기적으로 년평균 약 1억원의 경제적 효과 창출을 기대할 수 있다. 최근 무기체계는 전자장치 탑재가 증가되는 추세이다. 본 당사 혁신활동은 대부분 방산 전장 제조업체에서 적용 가능하다고 판단된다. 생산 및 검사공정 사각지대의 낭비요소와 개선대상을 식별 선정하여 혁신활동을 추진한다면 많은 방산업체의 발전과 나아가 K-국방력을 보다 더 확보 유지할 수 있다고 자부할 수 있다.