국방품질연구회(DQS)가 전하는 품질 인사이트
DQS 매거진
T-50 계열 항공기 Elastic Rod 품질결함 개선 연구
2023. 11. 10
글. 국방기술품질원 항공센터 항공1팀 이경찬 선임연구원
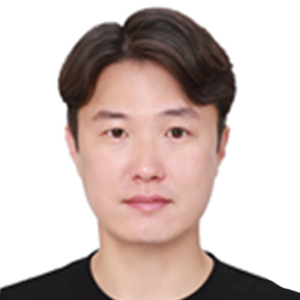
서론
초음속 항공기 착륙장치는 항공기가 이착륙하거나 지상 활주 또는 계류하고 있을 때 항공기 자체의 무게를 지지하는 장치로써, 항공기 중량 및 무게중심, 이착륙 속도 등을 고려하여 설계, 배치되어야 한다. 상세하게 주요 기능은 수평 및 수직 방향의 에너지를 흡수하는 역할을 하며, 수평 에너지는 브레이크에 의해 흡수되고, 수직 에너지는 Shock Absorber에 의해 흡수된다. 착륙장치는 1개의 Nose Gear와 2개의 Main Gear로 구성된 Tricycle의 형태이며 이와 같은 형태는 공기 지상활주(Taxing), 이륙(Take-off), 착륙(Landing)시 안전성과 이동성을 제공한다. 일반적으로 항공기 착륙장치의 피로 설계에는 안전수명 방법이 적용되며 균열이나 유해한 변형과 같은 구조적 결함이 항공기 운용수명 기간을 모사하는 피로 하중 스펙트럼 조건에서 발생하지 않아야 한다. 이러한 항공기의 피로 설계는 개발일정 및 비용의 영향으로 해석을 통해 피로 하중을 예측하고, 이를 검증하기 위한 최소한의 피로시험을 수행하는 것이 통상적인 착륙장치의 개발 과정이다 보니 실제로 국내에서는 전산 동역학 해석 소프트웨어인 ADAMS를 이용한 모델링 연구나 착륙장치 완충기의 충격흡수에 대한 모델링 해석을 수행하는 등 해석적인 영역에서의 연구가 대다수 진행되어왔다 [1]. 따라서 본 논문에서는 실제 운용 항공기 착륙장치에 발생된 결함을 바탕으로 파단면과 발생 원인을 분석하고, 비행 운용환경을 모사한 피로시험을 개선된 설계 형상에 적용하여 착륙장치의 건전성을 입증하였다.
본론
결함 현상
결함은 MLG(Main Landing Gear) 구조물 중 Elastic Rod 내의 스프링 링크에서 균열이 발생하였다. Elastic Rod는 특수 스프링 로드와 몇 개의 소형 링크로 구성되어 행정(Stroking)시에 휠축을 고정하여 MLG실 내에 타이어를 정확하게 위치시키는 역할을 하며, 상세 결함 부위는 아래 그림 1과 같다.
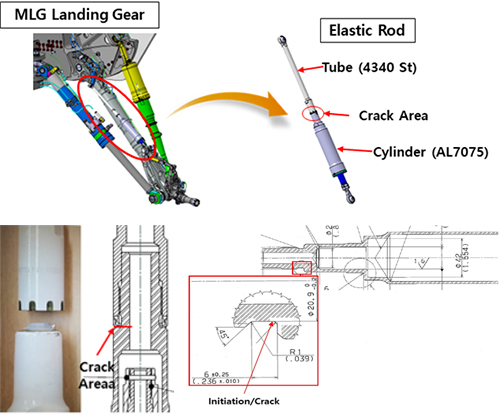
고장 탐구
그림 2의 Elastic Rod 실린더 파단부위에 대한 분석 결과 피로균열은 Tube 원주 외부에서 내부로 진전되었으며, 전체 원주 길이 대비 약 80%에서 다중시작점으로 시작됨을 그림 3과 같이 확인하였다.
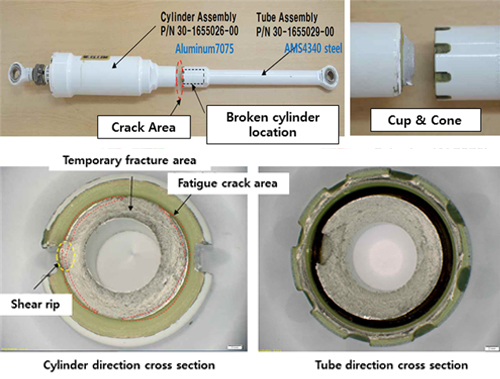
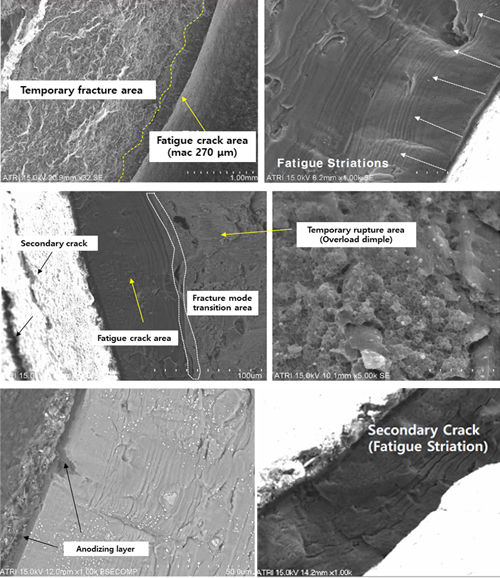
피로균열 발생부위 최대 깊이는 약 270 μm이며, 뚜렷한 피로줄무늬(Striation)가 시작 부위부터 관찰되는 등 다수의 Origin이 시작되는 특징을 고려한다면 비교적 높은 하중이 작용한 것으로 추정된다[2]. Dimple 방향(등축)의 일시파단 영역은 피로균열 진전(최대 0.3 mm) 중에 발생된 비정상적인 수직방향의 인장하중에 의한 것으로 보인다. 피로줄무늬 밀도(striation density) 분석결과, 전형적인 LCF(Low Cycle Fatigue) 현상이 관찰되었으며, 그림 4와 같이 Counting line 분석결과 500~600개로 계산되었다[3].
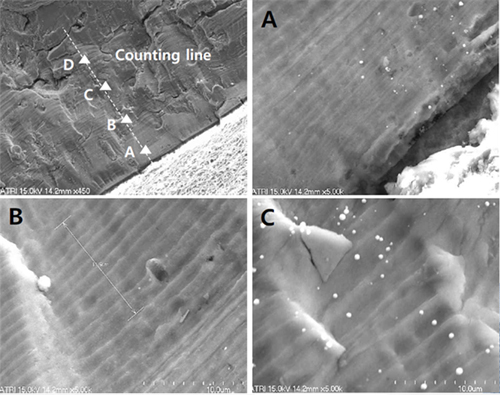
이러한 피로균열에 대한 근본적 원인 분석을 위해 개발 초기 Elastic Rod의 설계에 대한 검증이 필요하여 실제 운용 피로스펙트럼을 적용한 구조해석을 수행하였으며[4], 해당 조건 및 결과는 그림 5 및 표 1과 같다. 실제 피로수명에 대한 해석 결과는 설계 요구조건에 충족하는 것으로 확인되었다.
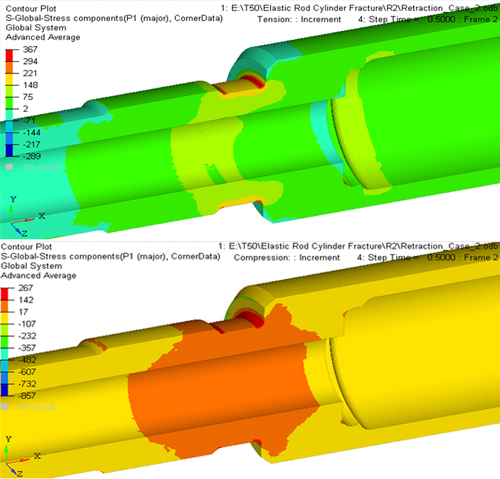
Division | Results | |
---|---|---|
Load Range | Max | 17,151 N (80%) |
Min | -15,194 N (80%) | |
Stress Range | S.max | 367 |
S.min | -267 | |
Equivalent Stress | 278 | |
Number of cycles | 179,057 | |
to failure | ||
Number of cycles | 24,637 Cycles | |
required | ||
Damage | 0.138 | |
Damage with | 0.55 | |
scatter factor 4 | (Good) | |
Safe Life | 44,764 | |
RF on Life | 1.82 |
표 1. 피로해석 결과
직접적인 피로균열 현상의 원인을 파악하기 위해 그림 6과 같이 동일계열 초음속 항공기 00대의 스프링 링크를 분해 확인한 결과 설계적으로 부적절한 Lock 와셔 형상으로 인해 체결 시 유격이 발생함에 따라 풀림 현상이 나타나 조립체 내부 피로 균열이 발생한 것으로 분석되었다. 적용된 Lock 와셔는 스테인리스 스틸 소재로 적절한 체결이 되지 못한 상태에서 반복적인 인장-압축 하중이 가해져 초기 상태 보다 상당히 두께가 감소한 형태의 변형이 발생하였음을 확인하였다.

품질 개선
발생된 결함을 개선하기 위해 기존 와셔의 재질보다 강성이 우수하고, 체결부에 정확한 토크를 적용할 수 있는 형태인 Cup 와셔 형상으로 표 2와 같이 설계 변경하였다.
Division | Before | After |
---|---|---|
Material | AISI 321 | 17-4PH |
Yield Strength | 205 Mpa | 1,000 Mpa |
700g | 30m | |
Configuration |
![]() |
![]() |
표 2. 설계 변경 전·후 형상
또한, 개선된 현상에 대해 설계적 타당성을 검증하기 위해 개선 전·후 형상으로 피로시험을 수행하였으며, 이번 시험을 통해 스프링 링크 체결부위의 피로균열 여부와 풀림토크를 확인하였다. 시험에 적용된 피로하중은 표 3과 같이 초음속 항공기 개발시 계산된 설계 허용하중과 비행시험 결과를 바탕으로 착륙속도에 따른 부가하중을 고려하여 산출된 인장 21,439 N, 압축 18,993 N을 적용하였다. 시험 Cycle은 설계요구도에 따라 24,637 Cycle/Life에 Scatter Factor 4를 적용하여 총 요구 수명주기는 98,548 Cycle로 설정하였다.
1 Cycle | Max Tension Load | Max Compression Load | Required Life |
---|---|---|---|
L/G Extension→Retraction | 21,439 N | -18,993 N | 24,637 |
표 3. 피로시험 요구조건
피로시험은 별도의 시험치구를 제작하여 개선전(Lock Washer)과 개선후(Cup Washer) 형상으로 수행하였으며, 1 사이클 시험이 끝나면 시험체를 피로시험기에서 탈거하여 시험체의 로드와 실린더 연결부위의 풀림토크를 측정하였다. 또한, 다음 사이클 시험을 위해 연결 위치를 정확히 마킹하고, 시험체를 분해 후 NDT 검사를 수행하여 균열 여부를 확인하였으며, 시험 결과를 표 4와 같이 정리하였다.
No. | Contents | Test#1 (Lock Washer) | Test#2 (Cup Washer) |
---|---|---|---|
(Lock Washer) | (Cup Washer) | ||
1 | Is there a crack in the cylinder connection before testing?(NDT) | No | No |
2 | Check Whether torque design requirements are met(750∼950 kgf·cm) | 780 | 780 |
3 | Measurement of loosening torque after 1 Life test | 720 | 920 |
4 | Check whether there are cracks in the cylinder connection area(NDT) | No | No |
5 | Measurement of loosening torque after 2 Life test | 710 | 900 |
6 | Check whether there are cracks in the cylinder connection area(NDT) | No | No |
7 | Measurement of loosening torque after 3 Life test | 450 | 800 |
8 | Check whether there are cracks in the cylinder connection area(NDT) | No | No |
9 | Measurement of loosening torque after 4 Life test | 400 | 820 |
10 | Check whether there are cracks in the cylinder connection area(NDT) | Yes | No |
표 4. 피로시험 결과
피로시험 결과 연성재질의 Lock 와셔는 토크 및 반복되는 인장-압축에 의한 두께 감소로 실린더 내부에서 발생되는 유격으로 인한 토크 풀림이 발생되는 것을 확인하였다. 이로 인해 4주기 피로시험 동안 개선전 형상인 Lock 와셔 타입은 토크 설계요구조건인 750~950 kgf·cm 벗어나는 결과가 나타나 최종적으로 실린더 연결부위에서 crack이 발생되는 것을 비파괴 검사를 통해 확인하였으며, 개선된 형상 Cup 와셔 타입은 설계 요구 수명 내에서 토크 풀림 현상 및 crack이 발생되지 않아 구조적 건전성을 입증하였다. 또한, 최적의 개선된 형상을 도출하기 위해 와셔의 두께를 (t=0.5, 0.6, 0.7, 0.8, 1.0 mm) 변수로 설정하여 풀림토크 시험을 추가적으로 수행하였으며, 두께 0.6 mm에서 풀림 토크가 815 kgf·cm로 가장 높은 시험 결과를 나타내어 설계 변경하였으며, 체결부 Peening 2개소 부위에 점토를 활용하여 토크를 지속적으로 유지할수 있게 그림 8과 같이 보강하였다.
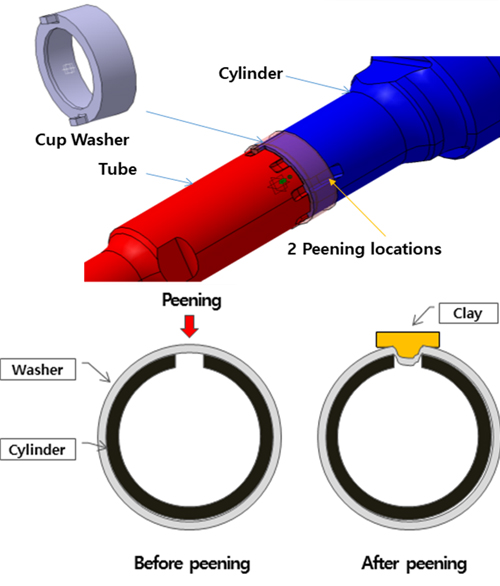
결론
본 연구는 초음속 항공기 착륙장치 스프링 링크에서 발생된 피로 균열에 대해 고장탐구를 수행하고, 설계 개선안을 도출하였다. 결함 발생 원인은 연성 재질의 Lock 와셔가 반복되는 인장-압축에 의한 두께 감소로 Tube와 Cylinder 사이에 토크 풀림과 동시에 유격 증가로 피로 균열이 발생한 것으로 분석되었다. 도출된 설계 개선안을 적용하여 피로 시험을 통해 기존 형상 Lock 와셔(450 kgf·cm) 대비 개선된 Cup 와셔의 풀림 토크(800 kgf·cm)가 약 1.78배 높게 나타났으며, 피로 균열 현상이 발생하지 않음을 검증하였다. 이러한 결과는 향후 유사 결함 발생 사례에 기초 자료로 활용될 수 있을 뿐만 아니라 향후 착륙장치의 신뢰성 향상을 위한 품질개선 연구에 활용될 수 있을 것으로 판단된다.
- 참고문헌
-
- 1. S. Choi, J. H. Lee, K. D. Cho and C. R. Jung, “An analysis on the ground impact load and dynamic behavior of the landing gear system ADAMS,” Journal of The Korean Society for Aeronautical and Space Sciences, vol. 30, no. 4, pp. 114-122, Dec. 2002.
- 2. D. H. Yoon, S. H. Na, J. H. Kim, H. Kim and D. Kim, "Evaluation of Fatigue Crack Propagation Behavior of Nickel-basedPowder Metallurgy Superalloy for Aircraft at Elevated Temperature," Transactions of the Korean Society of Mechanical Engineers A, vol. 41, no. 8, pp. 751-758, 2017.
- 3. Y. Murakami and K. J. Miller, "What is fatigue damage? A view point from the observation of low cycle fatigue process," International Journal of Fatigue, vol. 27, no. 8, pp. 991-1005, 2005.
- 4. J. J. Yun, S. W. Lee and T. H. Kim, “Assessment of Landing Gear Fatigue Impact Considering the Load Spectrum,” The Korean Society for Aeronautical and Space Sciences Spring Conference, pp. 662-664, 2016.