국방품질연구회(DQS)가 전하는 품질 인사이트
DQS 매거진
Microstructure Analysis를 통한 무인항공기 구성품 균열 원인 분석
2023. 12. 27
글. 국방기술품질원 항공센터 항공2팀 김대한 선임연구원
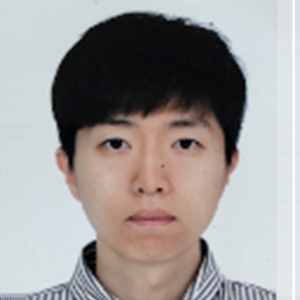
서론
현재 국내 무인항공기의 엔진은 기술력의 부재로 거의 해외수입에 의존하고 있다. 해외수입품의 경우는 해당 구성품에 문제가 발생하였을 때, 후속조치에 상당 시간이 소요되며, 해외 기술의 보안 등 문제로 원인분석에 대한 자세한 내용을 확인하기가 어렵다. 본 연구대상 무인항공기의 엔진도 해외수입품이며, 균열의 원인을 분석하는데, 제약이 많았다. 유인/무인 항공기의 엔진은 대부분 CSI(Critical Safety Item)이며, 문제 발생 시 비행안전에 치명적이다. 본 연구의 무인항공기 엔진 원제작사도 해당 결함을 인지하고, 구조적 문제에 대해서는 확인을 하였으나, 소재와 관련하여서는 전혀 언급도 없었으며, 정보도 제공받지 못했다.
그래서 기품원에서 주도적으로 소재와 관련하여 확인할 필요성을 인지하고, Microstructure Analysis를 통해서 균열의 원인을 도출하고자 하였다.
Microstructure Analysis를 위해서는 성분분석을 위한 장비, 광학/전자 현미경 등이 필요한데, 기품원 내에서는 해당 장비들이 부재하여, 시험은 KTR에 의뢰하여 진행하였다. Microstructure Analysis를 위한 시험 설계를 KTR과 협의하여 진행하였다.
연구 설계
Microstructure Analysis를 위한 시험으로 성분분석, 광학현미경(OM, Optical Microscope) 분석, 주사전자현미경(SEM/EDS, Scanning Electron Microscope/Energy Dispersive x-ray Spectroscope) 분석, 표면 경도 측정, Image Analyzer S/W을 사용한 금속간화합물(Intermetallic compound) 분율(fraction) 분석을 설계하였다. 성분분석은 ASTM E 1251-17a에 따라 Spark emission 방법으로 수행하였으며, 광학현미경은 HF, HCl 에칭 용액을 사용하여 에칭 후 확대 배율로 분석하였다. 그리고 주사전자현미경 분석은 확대 배율, EDS Mapping 분석을 수행하였다. 경도는 KS B 0811에 따라 Vickers Hardness를 측정하였다. 마지막으로 현미경 사진을 가지고 Image Analyzer S/W를 적용하여 금속간화합물의 분율을 측정하였다.
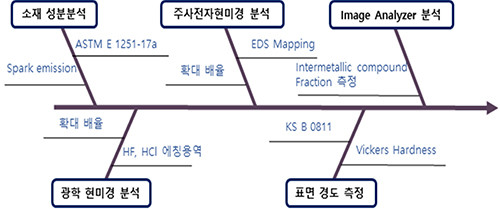
시편은 결함이 발생한 시편 3개(시편 A~C)와 발생하지 않은 시편 1개(시편 D)로 성분분석, 경도측정을 수행하였고, 이후 광학/전자 현미경 분석, 분율 측정은 결함이 발생한 시편의 대표 시편 C를 선정하고, 결함이 발생하지 않은 시편 D와 대조하면서 분석을 수행하였다.
연구 내용[1]
결함 현상
균열이 발생한 부위는 엔진에서 프로펠러와 엔진을 연결 해주는 구성품이며, 명칭은 엔진 프로펠러 허브이다. 이 허브의 키홈 부위에서 그림. 2와 같이 균열이 발생하였다. 해당 구성품은 해외수입 구성품으로 균열 발생 후 원제작사의 검토도 수행되었다.
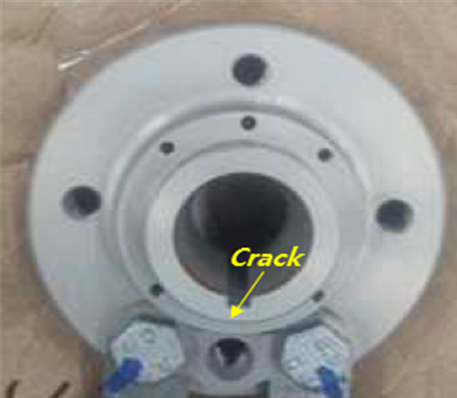
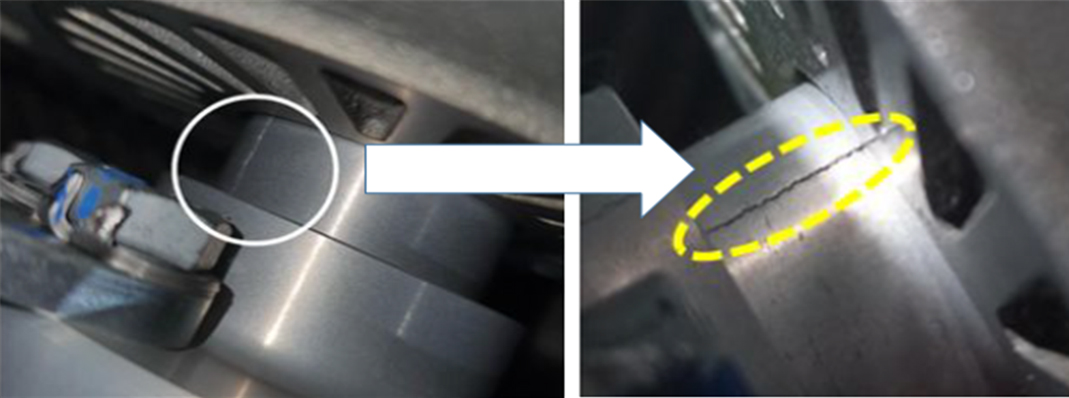
그림 2. 엔진 프로펠러 허브 균열 사진
그림. 2의 (a) 사진은 허브 전체사진이며, (b)는 균열이 발생한 부위를 확대한 사진이다.
성분 분석
결함이 발생한 시편과 발생하지 않은 시편 간의 성분차이를 확인하기 위해서 성분분석을 수행하였다.
성분 | A 시편 (%) |
B 시편 (%) |
C 시편 (%) |
D 시편 (%) |
---|---|---|---|---|
Si | 0.98 | 0.98 | 0.99 | 0.81 |
Fe | 0.49 | 0.48 | 0.49 | 0.25 |
Cu | 0.09 | 0.09 | 0.09 | 0.03 |
Mn | 0.81 | 0.80 | 0.80 | 0.50 |
Mg | 0.78 | 0.78 | 0.78 | 0.71 |
Cr | 0.03 | 0.03 | 0.03 | 0.11 |
Ti | 0.03 | 0.03 | 0.03 | 0.04 |
Al | 96.68 | 96.67 | 96.67 | 97.53 |
표 1. 성분분석 결과
표. 1을 보면 우선 A~D 시편 모두 동일한 성분이 나타나는 것을 확인할 수 있었다. 기본적으로 4개 시편 모두 Al Base 합금이지만 A~C 시편과 D 시편 간에 특정 원소의 성분함량이 다르게 나타났다. D 시편의 경우는 A~C 시편에 비해서 Si, Fe, Mn 함량이 다소 작게 나타나는 것을 확인할 수 있었다.
Si, Mn, Mg는 Al 합금에서 기계적 특성을 향상 시킬 수 있는 합금원소이므로, A~C 시편이 기계적 특성이 조금 더 높게 나타날 것으로 예상 할 수 있었다[2,3].
광학현미경 조직 분석
광학현미경 분석을 위해서는 표면처리인 에칭과정이 필요하다. 앞서 언급된 HF, HCl 용액을 사용하여 에칭한 시편의 분석을 수행하였다.
그림. 3은 저배율 광학현미경 이미지이며, ① ~ ③ 구역은 균열이 발생한 부위이고, ④ 구역은 균열이 발생하지 않은 일반 조직 부위이다. A~C 시편에서는 균열이 관찰되며, D 시편은 균열이 없는 것을 확인할 수 있다.
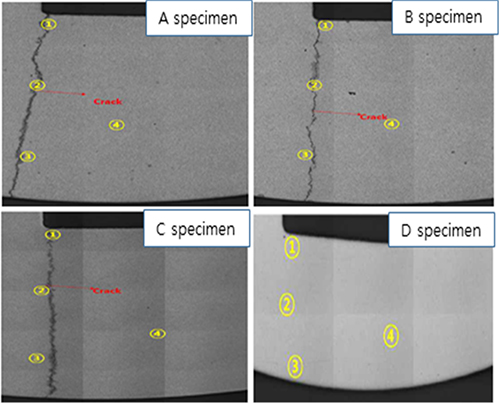
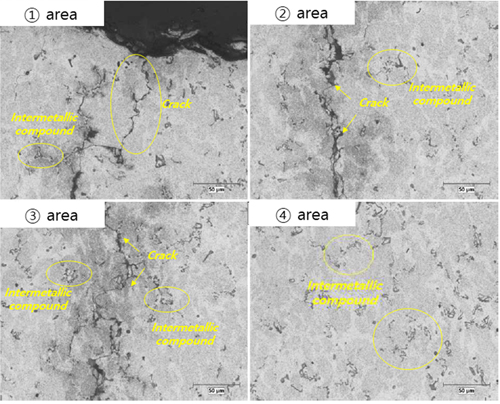
그리고 그림. 4는 고배율 광학현미경 이미지이며, 이미지에서 금속간화합물(Intermetallic compound)이 나타난다. 그리고 균열의 형상이 연결된 것이 아니라 단절되어 나타나는 것을 확인할 수 있다. 저배율 이미지에서는 균열이 연결된 것처럼 보였으나, 확대 이미지에서는 분리되어 있었다. 이것으로 볼 때, 초기 균열이 한 부분에서 발생해서 전파된 것이 아니라 다수의 지역에서 발생하고 전파되고 합쳐져서 최종 파단에 이르렀다고 추정할 수 있다. 그리고 금속 표면에 금속간화합물의 분포가 C 시편이 D 시편 대비하여 확실히 많이 나타나는 것을 확인할 수 있었고, 그 형상도 복잡한 형상이 많았다. D 시편의 금속간화합물 형상은 그림. 5와 같이 Rod-like 형상으로 나타났다. 이러한 C, D 시편의 금속간화합물 차이는 앞서 성분분석 결과의 합금원소 함량 차이에 기인한다고 판단된다.
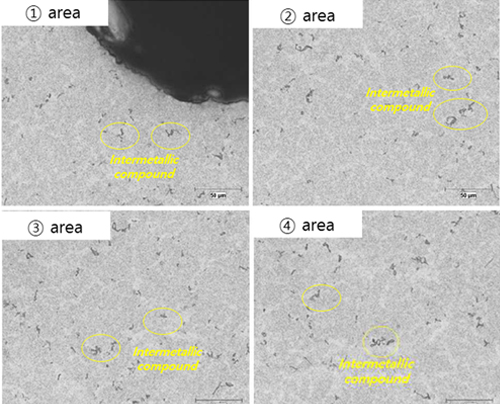
광학현미경 조직 분석
그림. 6은 C 시편의 확대된 주사전자현미경 이미지이고, 이미지에서 균열이 단절되어 나타나는 것을 확인할 수 있다. 광학현미경 이미지의 결과와 동일하였으며, 앞선 3.2. 장에서 설명한 균열 메커니즘으로 최종 파단이 발생한 것을 다시 한번 확인할 수 있다. 추가적으로 금속간 화합물 분석을 위해서 C, D 시편의 SEM-EDS 분석을 수행하였다(그림. 7, 표. 2, 3 참조).
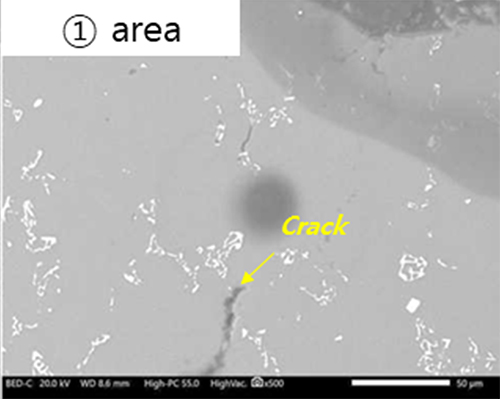
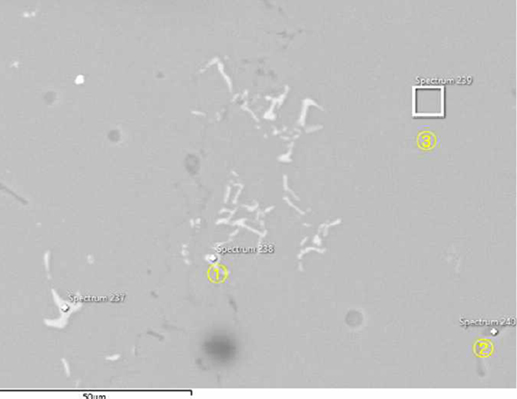
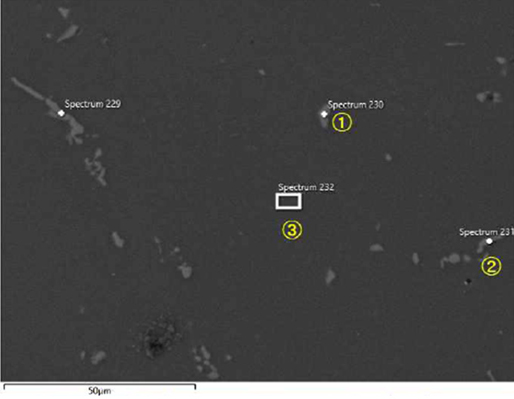
그림 7. 시편 C, D의 SEM/EDS 이미지
Element | ① Area (wt %) |
② Area (wt %) |
③ Area (wt %) |
---|---|---|---|
Mg | - | 31.36 | 0.63 |
Al | 62.73 | 46.84 | 98.50 |
Si | 8.24 | 21.80 | 0.56 |
Mn | 14.18 | - | 0.31 |
Fe | 14.84 | - | - |
표 2. 시편 C의 EDS 분석 결과
Element | ① Area (wt %) |
② Area (wt %) |
③ Area (wt %) |
---|---|---|---|
Mg | - | - | 0.65 |
Al | 75.95 | 64.59 | 98.77 |
Si | 6.65 | 8.40 | 0.58 |
Cr | - | 1.40 | - |
Mn | 7.62 | 9.68 | - |
Fe | 9.78 | 15.93 | - |
표 3. 시편 D의 EDS 분석 결과
표. 2를 보면 ① 구역에서 Al-Si-Mn-Fe의 화합물이 생성되었으며, ② 구역에서는 Mg-Si 화합물이, ③ 구역은 기지상만 나타남을 확인할 수 있다. 표. 3의 D 시편에서는 Mg-Si 화합물은 나타나지 않았으며, 주로 Al-Si-Mn-Fe 화합물과 기지상이 나타났다. 이러한 결과는 그림. 8의 EDS Mapping 분석결과에서도 확인 가능하다.
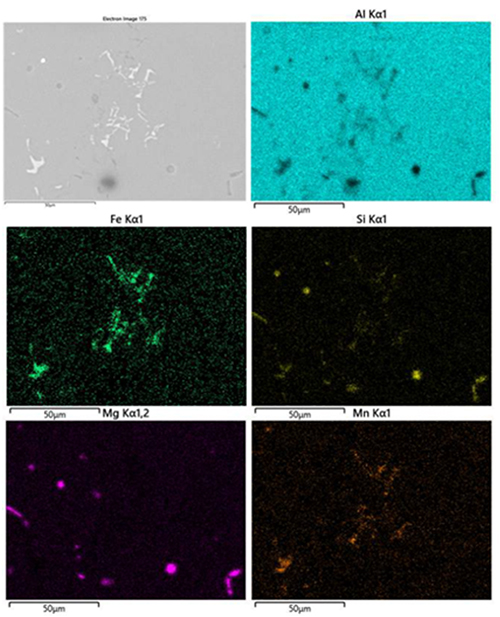
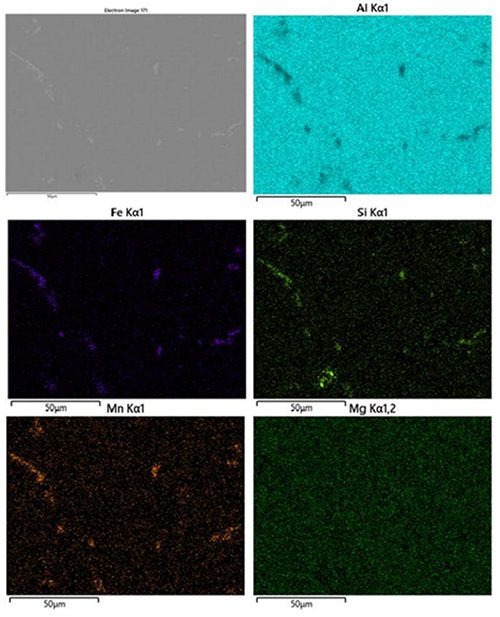
그림 8. 시편 C, D의 EDS Mapping 이미지
Image Analyzer 분석
금속간화합물의 분율(fraction)을 측정하기 위해서 Image Analyzer S/W를 사용하였다. 그림. 9를 보면 빨간색으로 표시된 부분이 금속간화합물이며, C 시편에서는 그 함량이 약 4.93%, D 시편에서는 2.20%로 나타났다. C 시편의 금속간화합물이 D 시편보다 약 2배정도 많은 것을 확인하였다. 이러한 사유로는 C 시편의 합금원소 함량이 D 시편보다 높아, 금속간화합물도 많이 생성된 것으로 사료된다.
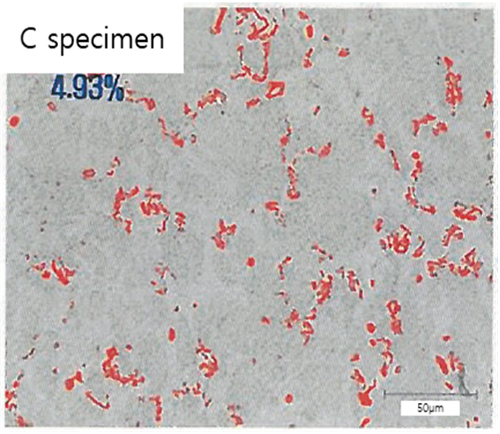
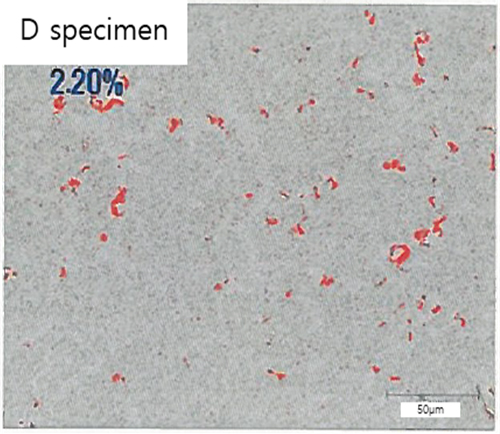
그림 9. 시편 C, D의 금속간화합물 분율 이미지
비커스 경도 시험(Hv)
시편들의 기계적 특성을 확인하기 위해서 경도 측정을 수행하였다. 총 4개의 시편에 대해 Vickers Hardness를 측정하였으며, 3회 측정 후 평균값을 계산하였다(표. 4 참조).
Specimen | Result 1 (Hv) |
Result 2 (Hv) |
Result 3 (Hv) |
Average (%) |
---|---|---|---|---|
A | 106 | 105 | 106 | 106 |
B | 107 | 105 | 108 | 107 |
C | 109 | 106 | 107 | 107 |
D | 93 | 96 | 97 | 95 |
표 4. 비커스 경도 시험 결과
표. 4의 결과를 보면, A~C 시편의 경도 평균값이 D 시편에 비해서 높게 나타나는 것을 확인할 수 있다. 이것은 A~C 시편의 원소함량이 높아, 표면에 금속간화합물이 많이 생성되고, 이것들이 높은 경도값을 얻을 수 있는 원인으로 볼 수 있다.
결론
무인항공기의 엔진 프로펠러 허브에서 발생한 균열의 원인을 도출하기 위해서 Microstructure Analysis를 수행하였고, 아래와 같은 결론을 도출하였다.
1. 성분분석을 통해서, 균열이 발생한 시편(A~C 시편)과 발생하지 않은 시편(D 시편)의 성분은 동일했으나, 시편 간 성분함량의 차이가 있고, 균열이 발생하지 않은 시편의 Si, Fe, Mn의 함량이 다소 작은 것을 확인할 수 있었다.
2. 균열의 발생 메커니즘은 초기에 여러 곳에서 다수의 균열이 발생하고, 그 균열들이 전파되고 합쳐지면 최종 파단이 발생하는 것으로 추정된다.
3. 광학현미경 및 전자현미경 분석 결과에 따르면, A~C 시편은 합금원소의 함량이 많아, 금속간화합물의 분율이 높으며, 형상도 복잡하게 나타났다. D 시편은 A~C 시편에 비해 합금원소의 함량이 낮으며, 금속간화합물의 형상이 Rod-like 형상으로 나타났다.
4. 이러한 금속간화합물의 영향으로 A~C 시편의 경도가 D 시편의 경도보다 약 10Hv 정도 높게 나타났다.
상기 결론과 같이 균열의 발생 유무에 따라서 미세조직적 차이가 나타났으며, 구체적인 금속간화합물의 분석을 위해서는 추가적인 미세조직 분석이 필요할 것으로 판단된다. 또한 이러한 미세조직적 차이를 최소화하기 위해서 금속의 성분함량 차이를 최소화한 원자재 관리가 필요할 것으로 판단된다.
- 참고문헌
-
- 1. D. H. Kim, J. H. Kang, "Analysis of the cause of crack in UAV through the microstructure analysis", Journal of the Korea Academia-Industrial cooperation Society Vol. 24, No.7, pp. 208-214, 2023
- 2. H. J. Kim, “Effect of Sc, Sr Elements on Eutectic Mg2Si Modification and Castability of Al-4wt%Mg-0.9wt%Si-0.3wt%Mn-0.15wt